PVDF Coated aluminum aluminium sheets coils
Specification of PVDF Coated
1. Aluminum coated coil alloy: AA1100,AA1050, AA3003, AA3004, AA3005, AA3105, AA5005, AA5182, AA5052, AA5754, AA5454, AA8011
2. Temper: O/H42/H44/H46/H48
3. Aluminum thickness (gauges): 0.02mm to 3.0mm
4. PVDF pre-painted aluminum coil width: 10mm to 1800mm
5 Coating: polyvinylidene difluoride (PVDF), no less than 25 micron for two times coating, three times coating 32micron.
6. Available colors: solid, metallic, marble, wood, anti-static, anti-scratch, etc
7. Coating hardness (pencil hardness): more than 2HB
8. Impact resistance: no cracking or peeling
9. Flexibility (T-bend): 2T
10. MEK resistance: more than 100 times
11. Further Processing: embossing, cutting to solid aluminium sheets, slitting to aluminium strips, etc
PVDF coating: 30 years guarantee
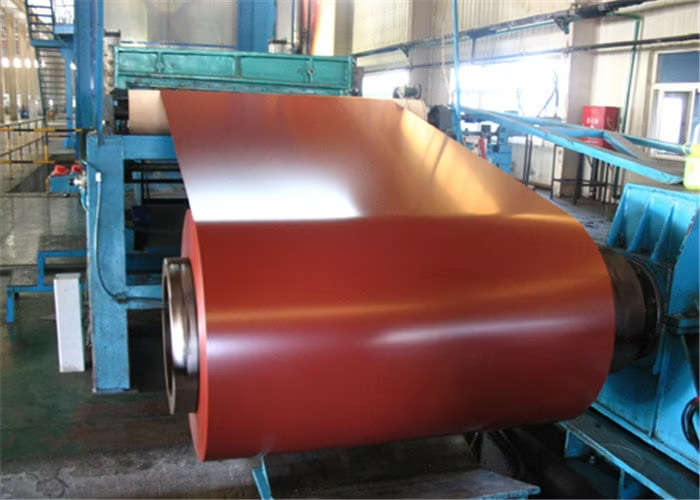
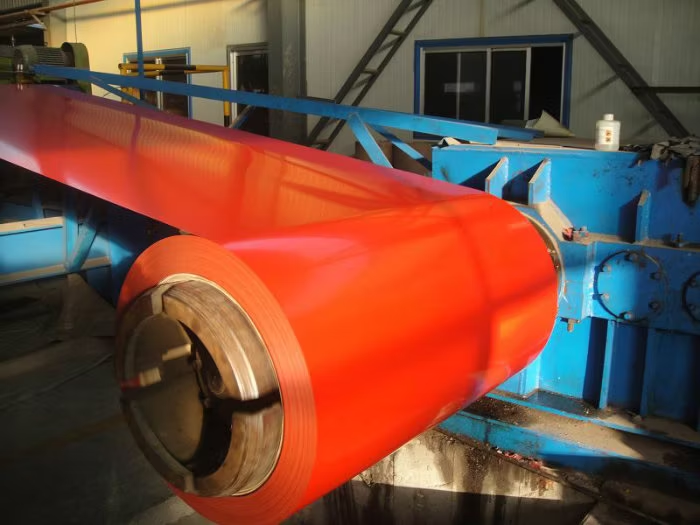
Three Coating Options
1. Self-clean Namo coating
With Namotechnology, our Namo PVDF coating could make it clean itself using sun and rain, maintenance and cleaning cost are reduced by at least 50%.
2. Durable coating
With our high-performance coating based on polymer resin, resistant to UV rays, moisture and abrasion. With such coating we can guarantee of up to 20 years.
3. Gloss coating
We have 3 gloss levels coating are available: High gloss, satin and matt.
PVDF Coating Compostion
To meet the industry's highest performance standards for architectural aluminum products, 70% PVDF resin-based coatings are recommended. The remaining 30% of the binder is composed of acrylic. Pigments, solvents and additives are also included in the formulated liquid product.
Polyvinylidene difluoride (PVDF)Painted Aluminum Coil applications:
From the roof to front door, PVDF resin-based coating protect and enhance numerous architectural aluminum products.
End-use include:
Aluminium roofing and wall panel systems.
Framing for curtainwall, windows, skylights and entrance systems
Louvers and grills, soffits, fascia, mullions, column covers and more.
TOP COATING
BACK COATING
Back coat epoxy blue
Good adhesion to adhesive and PU foam.
Good resistance to corrosion.
Back coat epoxy grey
Good adhesion to PE(composite panel)
Good resistance to corrosion
Specification of PVDF Coated
1. Aluminum coated coil alloy: AA1100,AA1050, AA3003, AA3004, AA3005, AA3105, AA5005, AA5182, AA5052, AA5754, AA5454, AA8011
2. Temper: O/H42/H44/H46/H48
3. Aluminum thickness (gauges): 0.02mm to 3.0mm
4. PVDF pre-painted aluminum coil width: 10mm to 1800mm
5 Coating: polyvinylidene difluoride (PVDF), no less than 25 micron for two times coating, three times coating 32micron.
6. Available colors: solid, metallic, marble, wood, anti-static, anti-scratch, etc
7. Coating hardness (pencil hardness): more than 2HB
8. Impact resistance: no cracking or peeling
9. Flexibility (T-bend): 2T
10. MEK resistance: more than 100 times
11. Further Processing: embossing, cutting to solid aluminium sheets, slitting to aluminium strips, etc
PVDF coating: 30 years guarantee
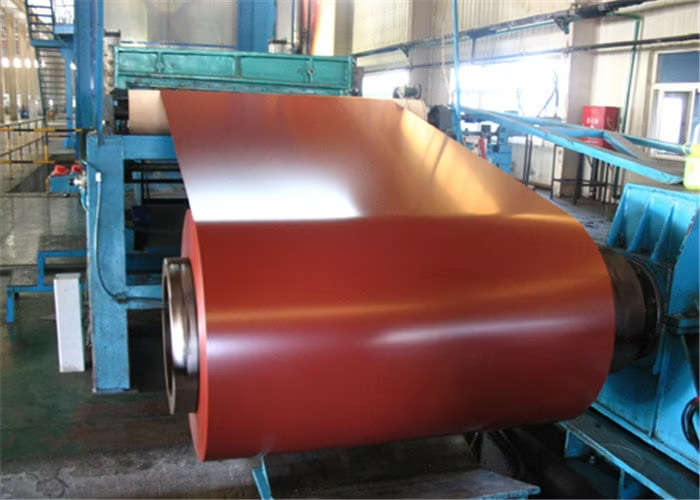
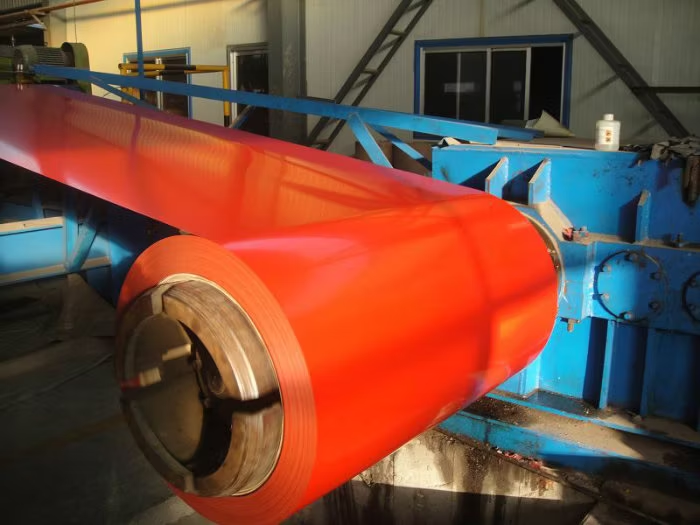
Three Coating Options
1. Self-clean Namo coating
With Namotechnology, our Namo PVDF coating could make it clean itself using sun and rain, maintenance and cleaning cost are reduced by at least 50%.
2. Durable coating
With our high-performance coating based on polymer resin, resistant to UV rays, moisture and abrasion. With such coating we can guarantee of up to 20 years.
3. Gloss coating
We have 3 gloss levels coating are available: High gloss, satin and matt.
PVDF Coating Compostion
To meet the industry's highest performance standards for architectural aluminum products, 70% PVDF resin-based coatings are recommended. The remaining 30% of the binder is composed of acrylic. Pigments, solvents and additives are also included in the formulated liquid product.
Polyvinylidene difluoride (PVDF)Painted Aluminum Coil applications:
From the roof to front door, PVDF resin-based coating protect and enhance numerous architectural aluminum products.
End-use include:
Aluminium roofing and wall panel systems.
Framing for curtainwall, windows, skylights and entrance systems
Louvers and grills, soffits, fascia, mullions, column covers and more.
TOP COATING
TEST | METHOD | RESULTS | |
Coating nature | PVDF | Standard PE | |
Thickness | ECCA T1 | Color:20±2um Primer:5+2um or according spec. | Color:18-2±2um, or according spec. |
Specular Gloss | ECCA T2 | Standard ±5% | Standard ±5% |
Color difference | ECCA T3 | ⊿E<1(Non-metallics colors) | ⊿E<1(Non-metallics colors) |
Polimerization | ILA-06 | >100 DF | >100 DF |
Pencil Hardness | ECCA T4 | ≥F | ≥F |
Impact | ECCA T5 | 100% | 100% |
Adhesion (Cross cutting+Erichsen) | ECCA T6 | >75% | >75% |
Bending | ECCA T7 | ≤2T | ≤2T |
Resistant to salt acetic acid spray test | ECCA T8 | 1000h/class 3 (According to EN1396/C 6.5)(Depends on specification) | 1000h/Class 1(According to EN 1396/C.6.5) |
Water immersion resistance | ECCA T9 | 1000h-B2S2 | ------ |
Resistance to QUVB test | ECCA T10 | 10 00 h Gloss Retention ≥90% ⊿E≤2 | 500h Gloss Retention ≥30% ⊿E≤5 |
Florida test | Class 3 (According to EU1396/C 6.3) | Class 3 (According to EU1396/C 6.3) |
BACK COATING
TEST | METHOD | RESULT |
Thickness coating | ECAA T1 | 5±2um |
Bending | ECAA T7 | ≤2T |
Polimerization | ILA 06 | >100 double roubs |
Adhesion after cross cutting | ECAA T6 | OK |
Adhesion after Erichsen | ECAA T6 | OK |
Resistance to Salt Spray | ECAA T8 | 1000 hours |
Back coat epoxy blue
Good adhesion to adhesive and PU foam.
Good resistance to corrosion.
Back coat epoxy grey
Good adhesion to PE(composite panel)
Good resistance to corrosion
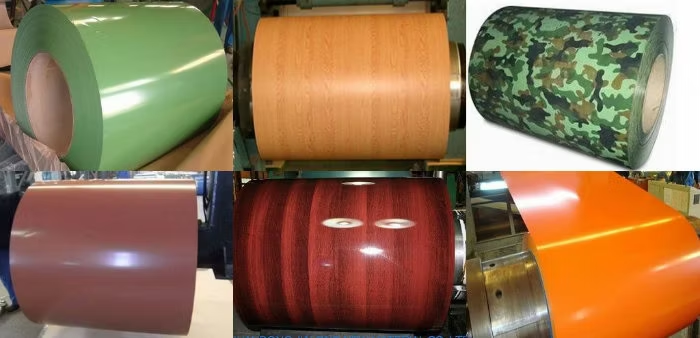